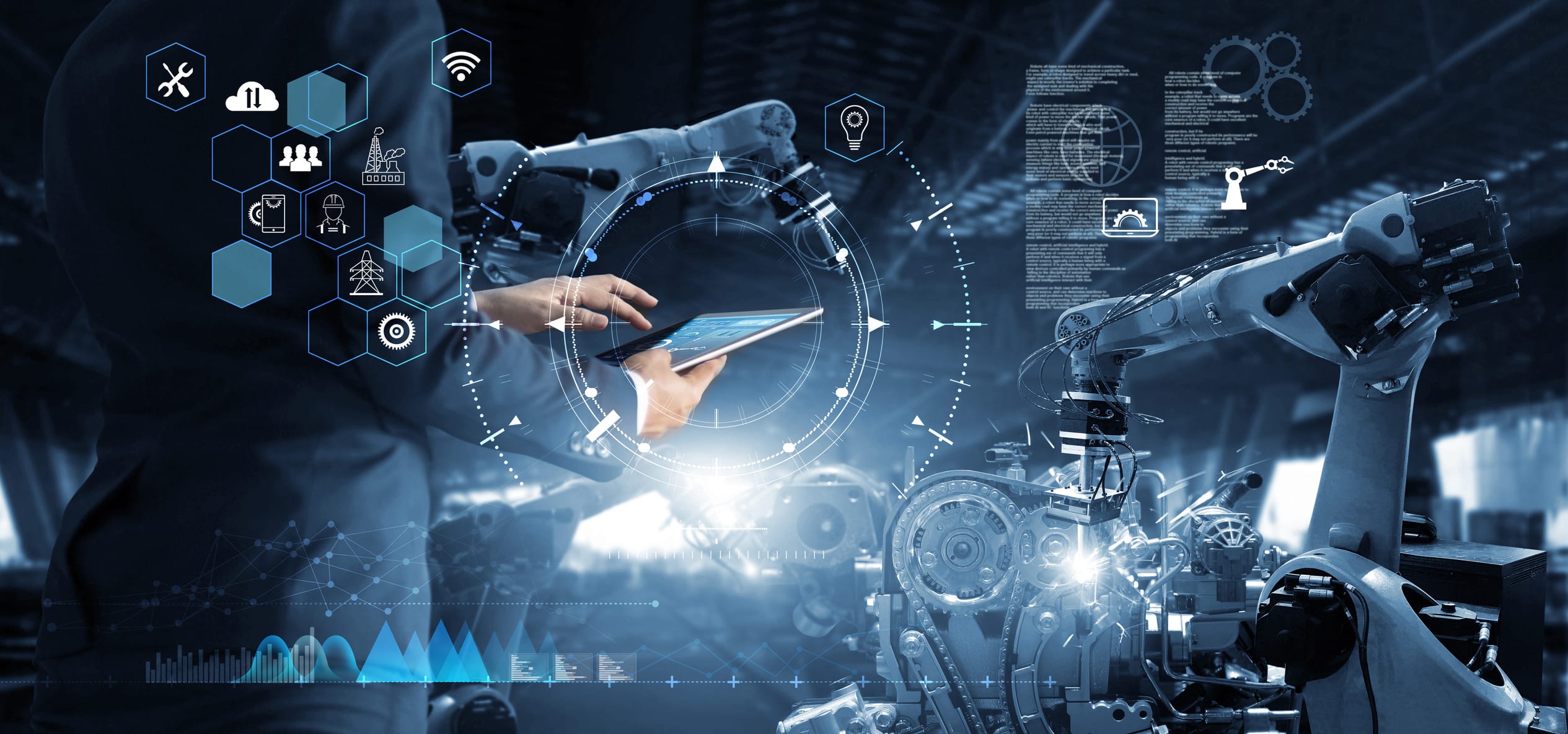
Smart Manufacture and Digital Transformation
At Ikusi, when we ask where a business can go through digital transformation, we are clear on the answer: up to wherever the customer wants.
As a technology-based company, we at Ikusi know that applying technology is merely a superficial aspect, and that true transformation entails assuming that technology is but a prelude to the evolution of current business models.
From the industrial point of view, the process is implemented these days by using the possibilities technology offers to compile critical data, process information in real time, identify patterns and respond accordingly, the process being understood as continuous, flexible and never static.
Let us, for instance, think of a company specializing in assembling automated production lines. What can the prospect of digital transformation offer it?
There are at least three angles from which processes of this sort may be approached. Where they can lead will depend, as I have pointed out, on what the customer wants and needs.
One of the ways of improving the value chain of a production line assembly company is monitoring the assembly itself, which redounds to the efficiency and effectiveness of the operative process, asset availability, product quality, and production capacity.
How is this interpreted from the viewpoint of digital transformation? By applying technology, such as an IIoT (Industrial Internet of Things) platform to provide real-time data on both the behavior of every individual asset comprising a production line and an overview of the whole line, enabling the detection of potential anomalies well in advance.
A second transformation phase entails automating the design of the production lines themselves, which may be handled by incorporating a digital twin to improve the quality of products offered and the positive perception of customers about the products and services provided.
We are talking about knowing the customer experience in using the “automated lines” delivered and their behavior in order to deal with the continuous improvement of production line design based on these qualified data. Once more, the technological method used is the IIoT platform.
Let us imagine we are dealing with a company open to change that wants to progress further in its transformation process, providing services associated to the sale of the automated lines it specializes in – a company open to incorporating new business models that seeks to expand its offer by bringing greater value to its clients through remote production line monitoring “as a service”.
This is what is known as a “servitization” project, one of the pillars of Industry 4.0, which consists of offering services related to products in order to gain in competitive advantage.
One of the key values could be offering the clients from the automated production line company key information on its production by developing a customized application enabling them to learn and continuously monitor the operating parameters of their lines and of each of the machines comprising these, the associated KPIs, the alerts generated, and even – by incorporating predictive analysis – offering the early detection of anomalies.
Based on productivity, availability and quality KPIs, OEE (Overall Equipment Efficiency) is calculated for each machine and for the entire line. New business lines are thus once more created by deploying an IIoT platform, which increases productivity and improves the availability of these customers’ assembly lines.
These are three perspectives to digital transformation where technology is a tool, and where what is important is to identify how processes may be transformed, how efficiency may be increased, and how the foundations of businesses may be changed to create more value by applying technology.