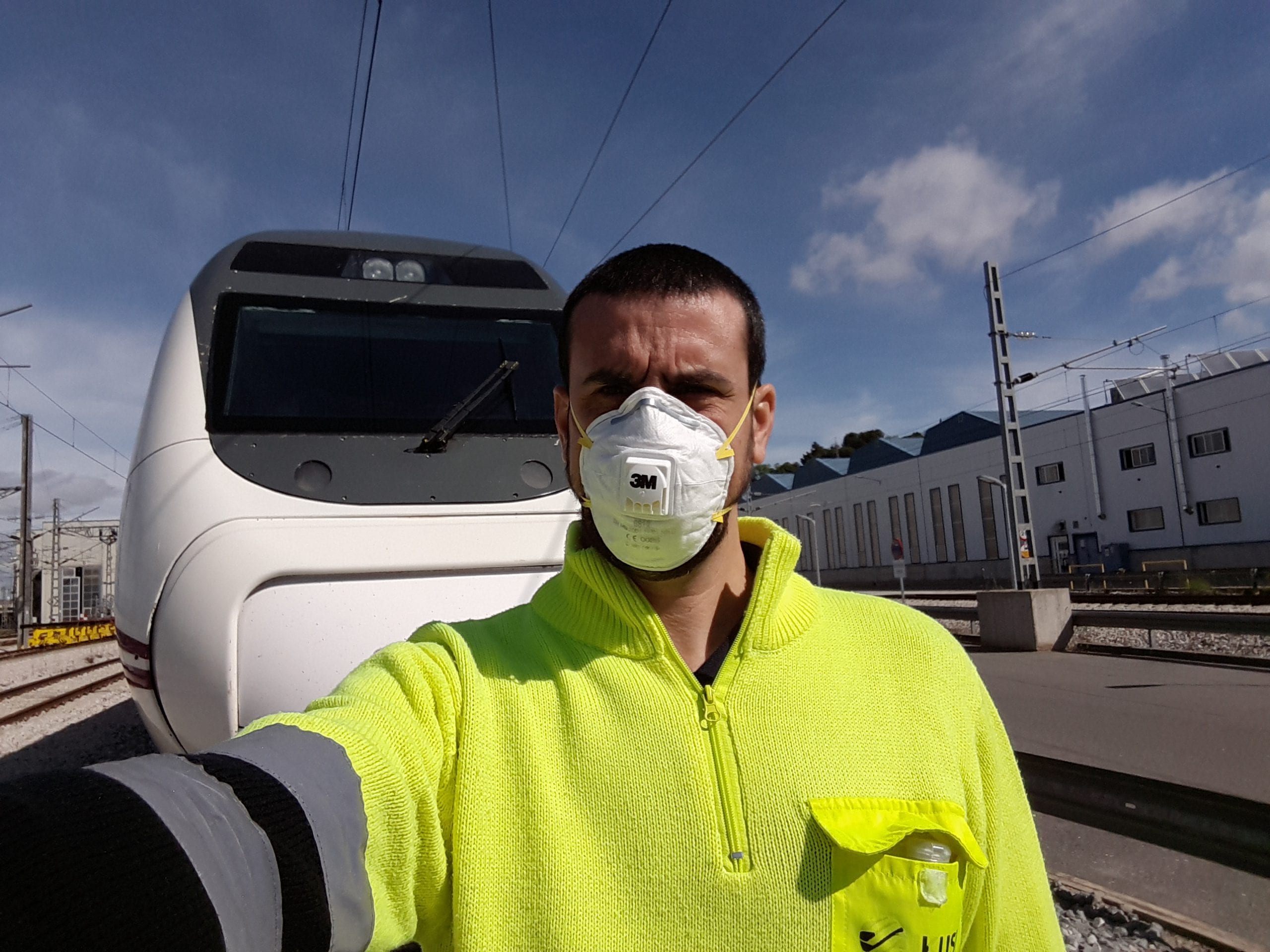
Interview Alberto Rodriguez, technical coordinator
Alberto was used to living on the road to perform maintenance and system evolutions mainly for Actren and Talgo. When necessary, he responds to customer incidents thousands of miles away like Siteur or Bombardier in Mexico. As technical coordinator, he is in charge of responding to incidents or performing system evolutions inside the trains themselves. He continues to do so, although without moving from one province to another and now with greater availability to work on the trains themselves, mostly with mobility restrictions due to the COVID-19 crisis.
You told me that your work requires multiple journeys and that now with the health crisis they have been considerably reduced
That’s right. I was used to constant displacement. I’m the technical coordinator of the onboard business and the main projects I work on are maintenance and systems evolution for Actren and Talgo. Therefore, my working life was spent on continuous trips to the facilities of these two companies, which forced me to travel to Galicia, Barcelona, Toledo, or to move from the offices of Ikusi in Getafe to other areas of Madrid.
It is a job very close to the client with multiple meetings, incidents, and the need to give a quick response. Transport is essential and the trains have to be operational. From Ikusi we provide service to more than 100 trains.
However, during the coronavirus crisis, rail transport has decreased considerably.
That’s true. But we must continue to perform maintenance service. The current time has some advantages. Before it was more difficult for the train to be available for maintenance or to test the systems, now you just have to ask, since 80% of the fleet is stopped.
How is your work developing from a health and safety point of view?
Logically, we adopt all the safety measures using a mask, gloves, or disinfectant gel. In that sense, we also find far fewer workers from the customers in the workshops and on the trains themselves, so we can do our work while keeping a safe distance, when in a normal situation the Actren and Talgo workshops are a constant coming and going of people.
What is the most rewarding part of your job?
We have a very close relationship with the customer. We look for solutions to their needs for technological evolution and maintenance. Based on the data from the systems, we are able to analyze what the main incidents are, why they occur, how they can be solved… And we are making progress in remote maintenance systems, we already have a prototype, so that we can connect directly to the train online without having to physically go to the workshops. The customer appreciates this proximity and recognizes our work. And that is very gratifying.